事業内容business
加工の技術と工程
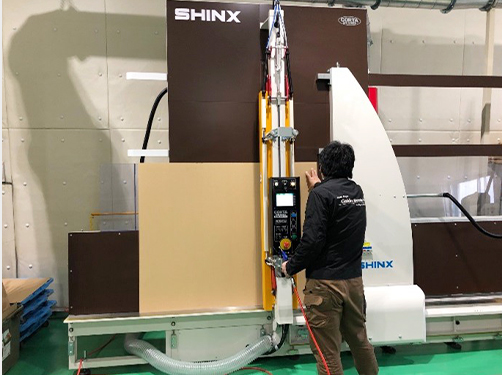
切断
アクリル・塩ビなどの原板を寸法切りする工程です。
製品を製作していく上で重要な作業です。
パネルソーでカットしていきます。
デジタル定規を使用し高精度の寸法出しが可能なこと、また自動送り機能も付いていることから作業性が良く、作業効率が高いことも特長です。
削る
プレーナー(カンナ)で切断面を削り、滑らかに仕上げていく工程です。
パネルソー(ノコ)でカットした切断面は粗く、見た目や手触りも良くなく、接着加工にも影響があるため、表面を美しく整えるプレーナー仕上げを行った上で、バフ磨き加工や接着加工を行います。
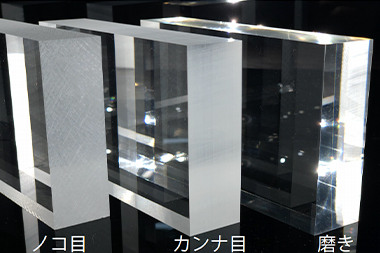
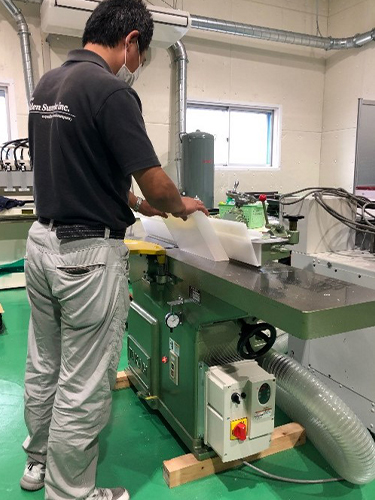
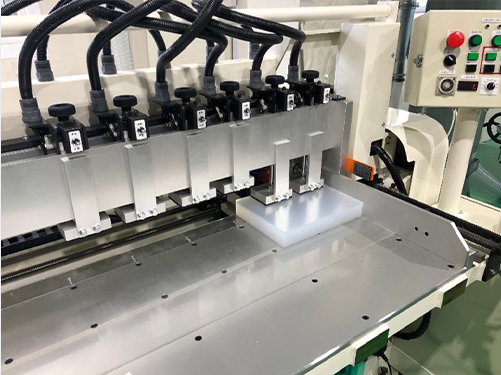
磨く
切断面を磨く工程です。アクリルの特性である透明度を引き立てます。
鏡面加工機・バフで磨き加工をしていきます。
ダイヤ刃(単結晶)で削っていくので、鏡面加工機での仕上がりは他の加工機より美しく仕上げることができます。
軸傾斜付きの機械なので、C面部分の磨きも可能です。
また鏡面加工機で加工できない部位はプレーナーや切削加工後にバフで磨いていきます。
※バフでも届かない部位の場合は、コンパウンドで手磨きやブラスト加工で磨く場合もあります。
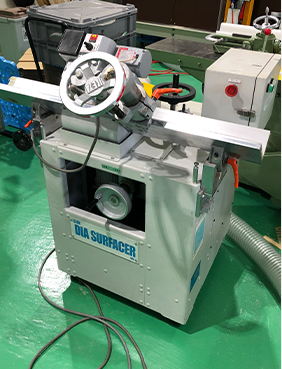
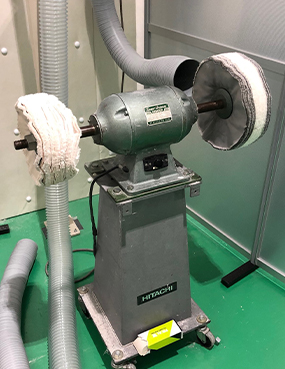
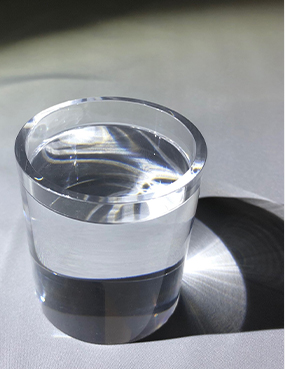
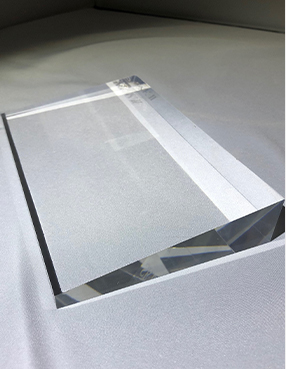
切削加工
アクリル・塩ビなどにCADデータ・治具を使って外周・穴・溝を切削していく工程です。
NCルーター・マシニング・NC旋盤などで加工するため、切削形状が異なっても、ツールチェンジにより1回のセットで多種の加工が可能です。
またダイヤ刃(単結晶)を用いて加工することで鏡面加工も可能になります。
卓上のルーターマシンは治具にセットし部分加工および重ね加工ができるので、精密品には不向きですがコストを低く抑えられます。
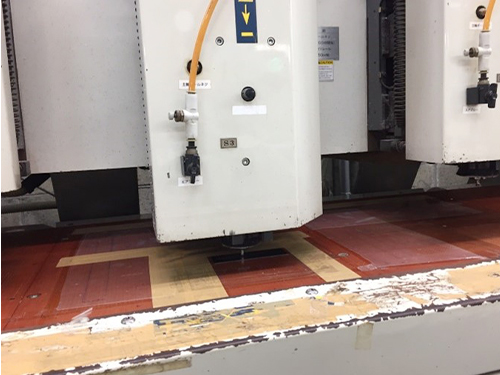
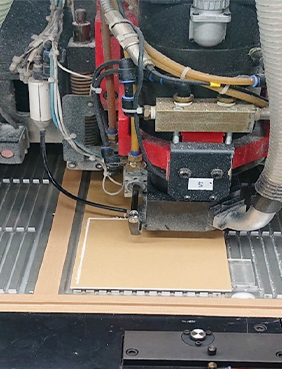
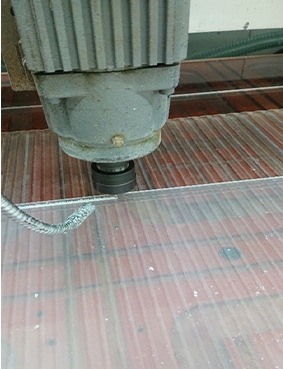
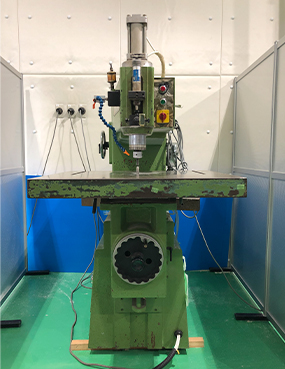
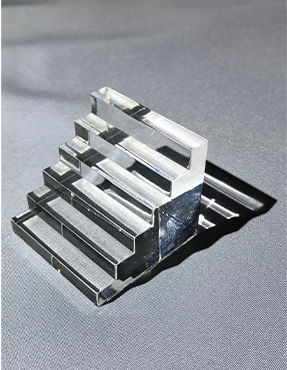
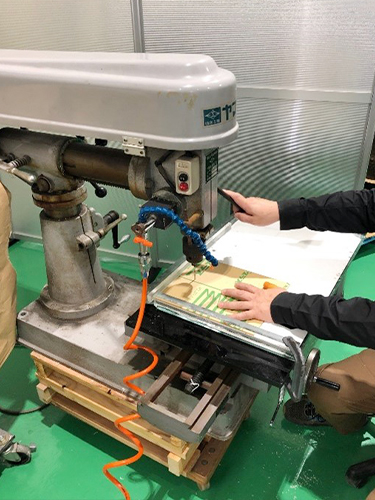
穴あけ
ボール盤で穴あけをしていく工程です。
位置決めした場所で板を重ねて加工していくことができます。
ビス用の皿穴の加工や、100分の1単位のドリルもあるので、ネオジム磁石などが打ち込み可能な細かなサイズの加工も可能です。
面取り
アクリル・塩ビなどの切断部分の鋭い面を取っていく工程です。
卓上面取り機・プレーナーを使用して面取りを行っていきます。
またNC加工で形状加工と面取りを同時に行うこともできます。
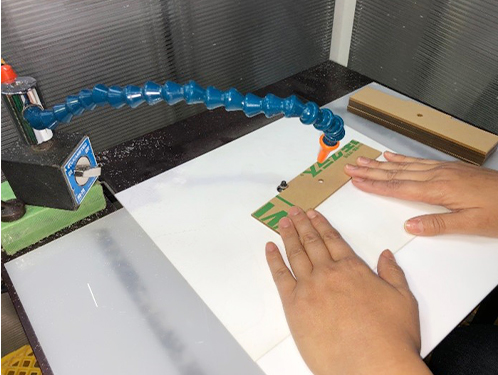
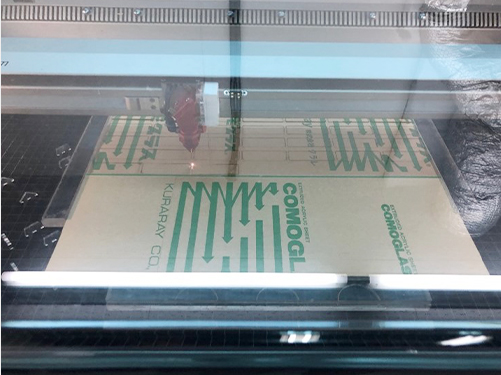
レーザー加工
レーザー加工機による、切断・彫刻をする工程です。
アクリル15tまで切断することが可能です。
(協力会社の設備で30tまで切断可能)
一度の工程で切断・彫刻を組み合わせて作業でき、磨きがかかった美しい切断面に仕上げられます。
彫刻は細かな柄や文字を彫ることができます。
LEDを組み合わせて光らせる場合は、特殊な彫刻方法でムラなく美しく光らせることも可能で、照度アップもできます。
また搭載のCCDカメラで丁付けされた印刷物のマーカーを読み取り、位置ズレのないスムーズな作業を行うことができます。
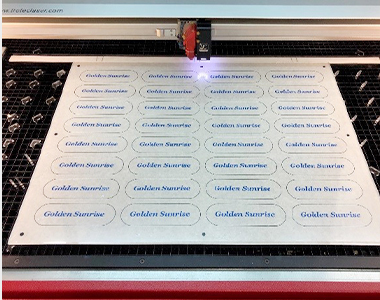
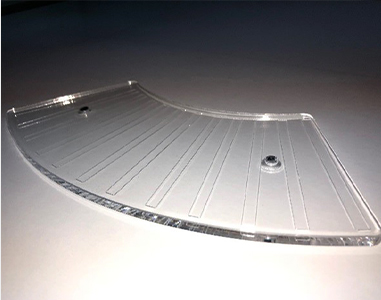
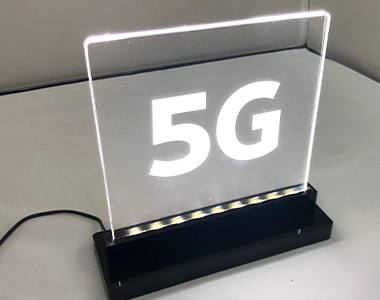
接着・組立
切断した板を接着して貼り合わせる工程です。
注射器で溶剤を流し込み溶かし合わせて接着していきます。
ディスプレイ製品を組み立てる上で最も重要な作業になります。
寸法切りした板を治具に合わせて配置し、寸法・形状に沿って組み立てていきます。
特に透明の板を接着する場合、気泡が入ったりムラになったりしやすいので慎重さと技術が必要となります。
作業工程をうまく組んで、作業性や精度の高い治具を使用することでクオリティを保ちつつ生産性を上げ、量産品の低コスト化を図っています。
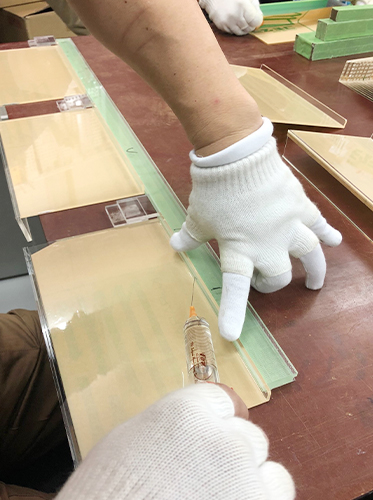
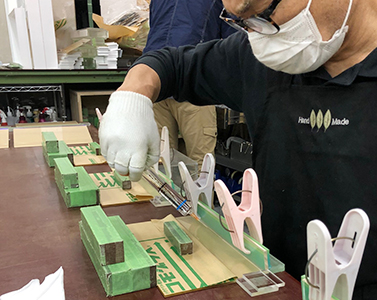
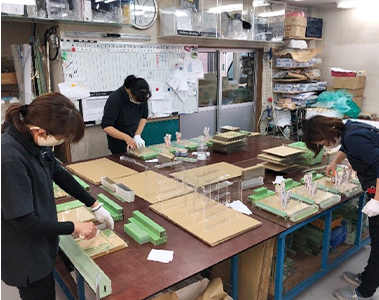
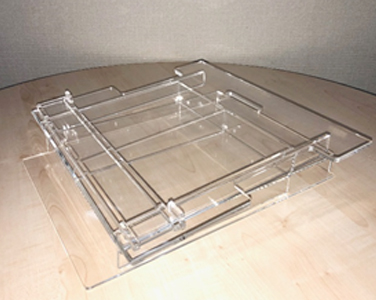
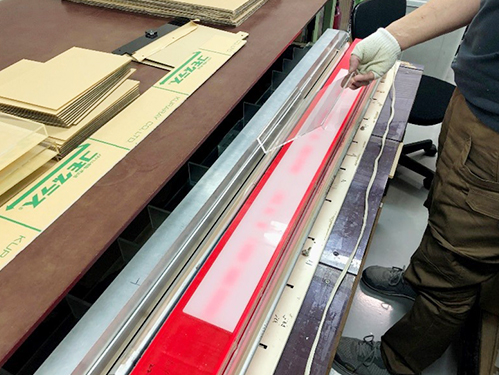
曲げ加工
板を加熱し軟化させ曲げていく工程です。
熱曲げ専用のヒーターを使い一定の温度に熱することで、加熱箇所がやわらかくなり治具や型にはめてR形状にすることができます。
デザインを目的にR形状にする場合もありますが、塩ビ・PETなどの薄板を曲げることにより商品台などの強度を増すことができます。またプライスカードを立てるスタンドなどを安価で製作できるため、よく利用されています。
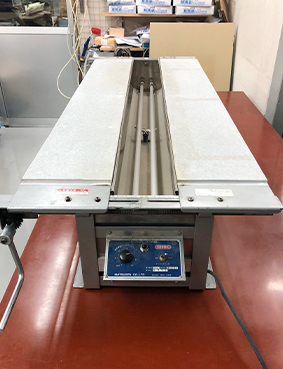
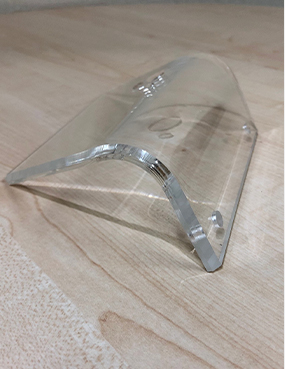
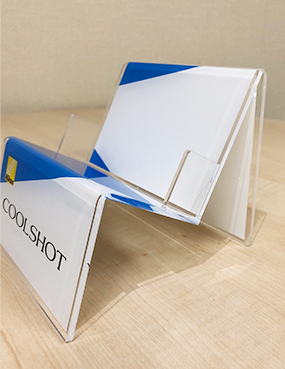

梱包・アッセンブリ・出荷
完成した製品の検品・清掃・箱詰めなどを行う工程です。
キズ・ワレ・ズレ・接着不良などを検品し、除電・清掃して袋・エアキャップに詰め梱包していきます。
同梱する印刷物や商品などのセット梱包もお引き受けします。
物量の多い場合はパレットで倉庫に保管して出荷いたします。
全国への出荷・発送を承っております。
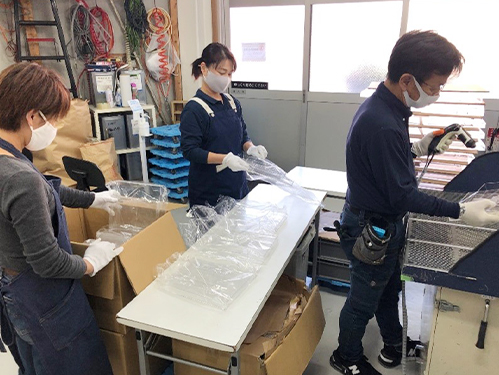
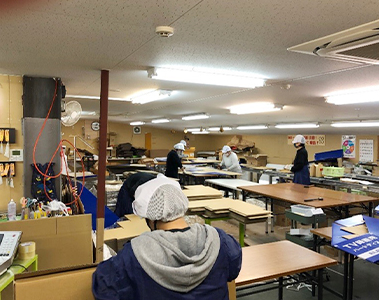
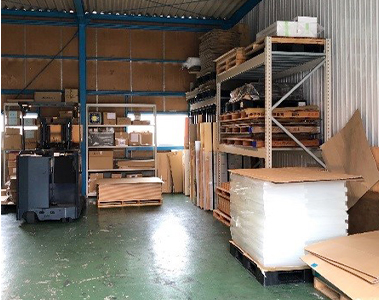
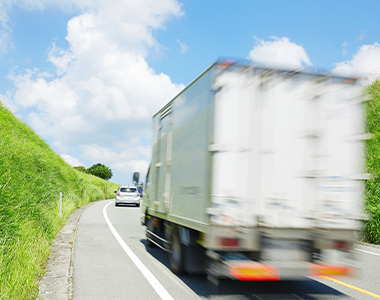